The European Union's Annex 1 regulation, which outlines the requirements for properly and safely manufacturing sterile medicinal products for human and veterinary use, has recently undergone significant revisions since its first publication in 2007. Annex 1 applies to all sterile medicinal products manufactured in and exported to the European Union and the UK.
General guidance provided by this Annex must be followed in the design and control of facilities, equipment, systems, and procedures by applying Quality Risk Management principles to prevent microbial, particulate, and endotoxin/pyrogen contamination. This regulation covers the range of product types, including active substance, excipient, primary packaging material, and finished dosage form, from manual processes and highly automated manufacturing systems. Also included are biotechnology, classical small molecule manufacturing systems, and closed systems.
Understanding the revisions to the Revised EU Annex 1 Regulation
The revised EU Annex 1 regulation focuses on better managing risks, monitoring and controlling sterile environments, properly training employees, and how to use specific equipment. The revision of Annex 1 was published last year and will come into force on August 23, 2023.
The GMP/GDP Inspectors Working Group and the PIC/S Committee jointly recommended that Annex 1 be revised to reflect changes in regulatory and manufacturing environments. The revisions remove ambiguity and inconsistencies by taking account of advances in technologies, including tools described in the ICH Q9 and Q10 guidelines.
It’s important for pharmaceutical companies to understand and follow these changes to make sure their products are made safely and of the highest quality. The revised annex reinforces quality risk management principles and mentions the contamination control strategy. The scope has expanded beyond just sterile products to cleanroom classifications, design of premises, validation, monitoring, and personnel gowning.
For manufacturing sterile products, the Annex outlines four grades of cleanrooms or zones for pharmaceutical companies. This ranges from Grade A for the highest level of cleanliness required to Grade D for less stringent sanitization requirements. Changes have been made to the requirements for PPE for each clean space.
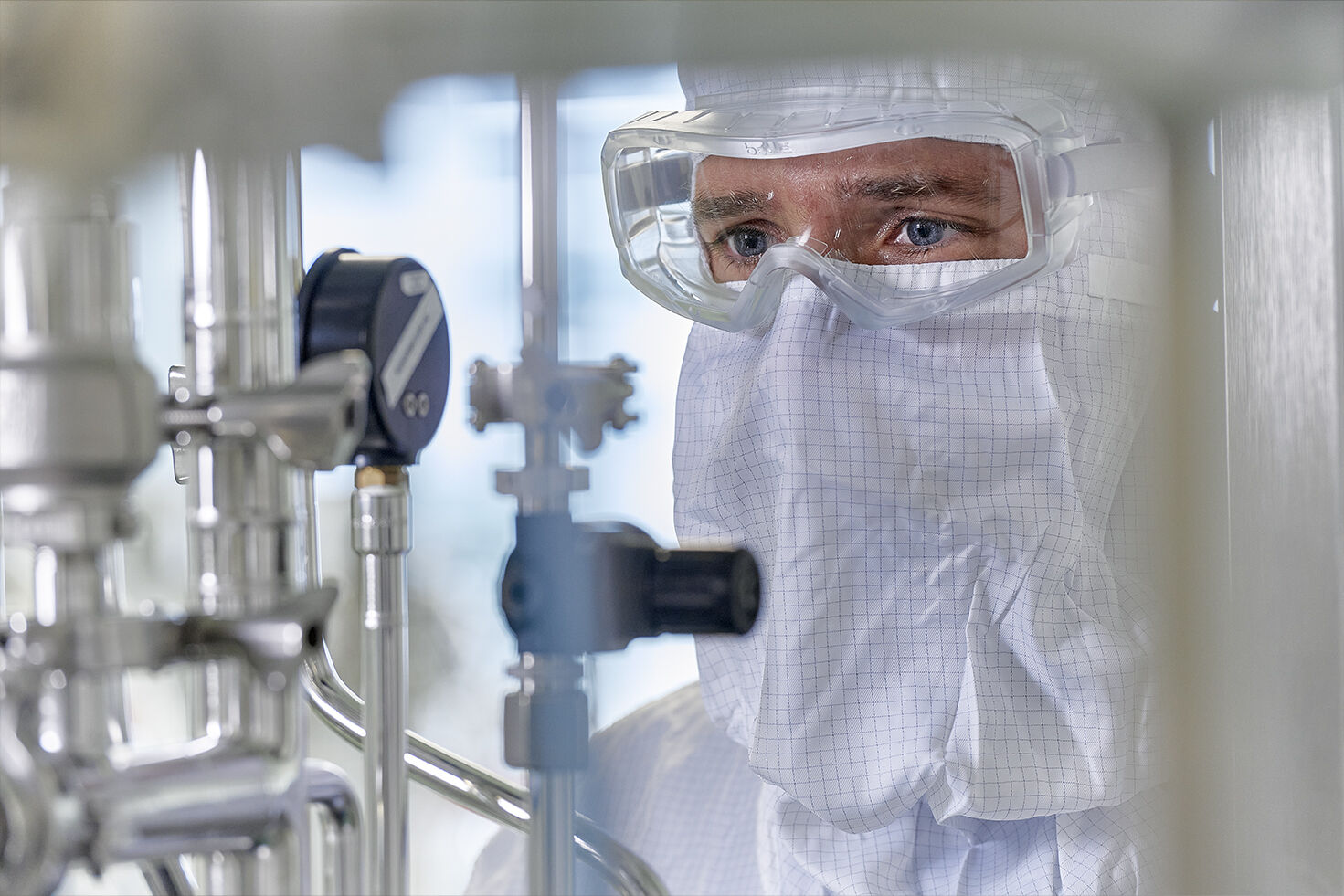
Personal protective equipment changes in the Annex
The revised EU Annex 1 regulation brings more attention to managing risks that could cause contamination. The personal protective equipment (PPE) of lab workers and other personnel is essential for safety, cleanliness, and compliance with the new regulations. Equipment protects both the environment and the wearer.
Focus is paid to using sterilized eye coverings such as goggles in the revised Annex. Eye protection is crucial for keeping employees safe and maintaining a clean environment. Using goggles with indirect vents offers better protection against airborne contaminants, splashes, and other hazards.
There is further clarification for gowning requirements. The revised Annex lists six types of non-woven fabrics to be used in cleanrooms along with their barrier properties, splash resistance, and air and moisture permeability. There is additional guidance in the Annex for qualifications of employees and how to properly train staff to maintain sterile conditions.
Requirements of the Annex include:
7.11: Cleanroom clothing quality should be appropriate for the processes and grade of the area. Attention should be paid to ensure eye coverings are subject to the sterilization process. Packaging should be visually inspected before use and reusable eye coverings should be replaced once damaged and at a set frequency determined by qualification studies.
7.13: Clothing, eyewear, and PPE requirements for each cleanliness grade are given below:
Grade B (including access into grade A):
- Sterile facemasks and eye coverings, for example, goggles, should be worn to cover and enclose all facial skin to prevent the shedding of droplets and particles
- Appropriately sterilized footwear, such as over-boots
- Sterile headgear should enclose all hair, including facial hair
- Protective clothing should minimize shedding of fibres and participles
- Second pair of sterile gloves worn over pair worn while donning PPE
Grade C:
- Single or two-piece trouser suit gathered at the wrists and with a high neck
- Appropriately disinfected shoes or overshoes
- Hair, beards, and moustaches should be covered
Grade D:
- General protective suite
- Appropriately disinfected shoes or overshoes
- Hair, beards, and moustaches covered
Note that gloves and facemasks may be required in grade C and D areas when doing activities considered to be a contamination risk as defined by the Contamination Control Strategy (CCS).
7.15: Operators entering grade B or A areas should gown in sterilized protective garments including eye coverings of an appropriate size at each entry. Sterilized gowns should have a maximum wear period before replacement during a shift as defined as part of the garment qualification.
Impacts on pharmaceutical companies and production processes
Eye protection plays a crucial role in mitigating the impacts of the revised EU Annex 1 regulation on pharmaceutical companies and their production processes. While the changes may lead to increased costs and production delays, ensuring compliance is vital for maintaining the quality and safety of medicinal products.
The Annex strongly recommends the use of machines to minimise contamination and emphasises the need for automation on the manufacturing line. This approach necessitates the implementation of new processes and equipment, potentially resulting in additional costs.
The revised Annex also provides guidelines for cleanroom design, specifying factors such as ceiling shape, materials, and the flow of objects, people, and air between clean zones. Utilising positive and negative pressure rooms, airlocks, and filters helps to minimize contamination risks. Furthermore, the language has been reinforced regarding the use of separate change rooms for entering and leaving grade B areas.
Processes must be meticulously documented and traceable, with senior management overseeing and regularly reviewing risk management strategies. These requirements may introduce delays in production due to the need for extra testing and documentation.
By emphasising the importance of eyewear protection, pharmaceutical companies can effectively address the impacts of the revised Annex 1 regulation, safeguarding their production processes and ensuring the quality and safety of their medicinal products.
Importance of quality and safety
Due to changes in regulatory and manufacturing environments, including advances in technologies, the Annex 1 regulation has been revised to prevent microbial, particulate, and endotoxin/pyrogen contamination. This includes changes to the use, wear, and replacement of vital PPE, including eyewear.
Eye protection is vital for pharmaceutical companies to comply with the revised EU Annex 1 regulation. Despite increased costs and production delays, companies can choose from single-use or autoclavable options based on contamination risks and sustainability considerations. Compliance with eyewear protection measures helps meet regulatory requirements and maintain a balance between short-term challenges and long-term sustainability goals.
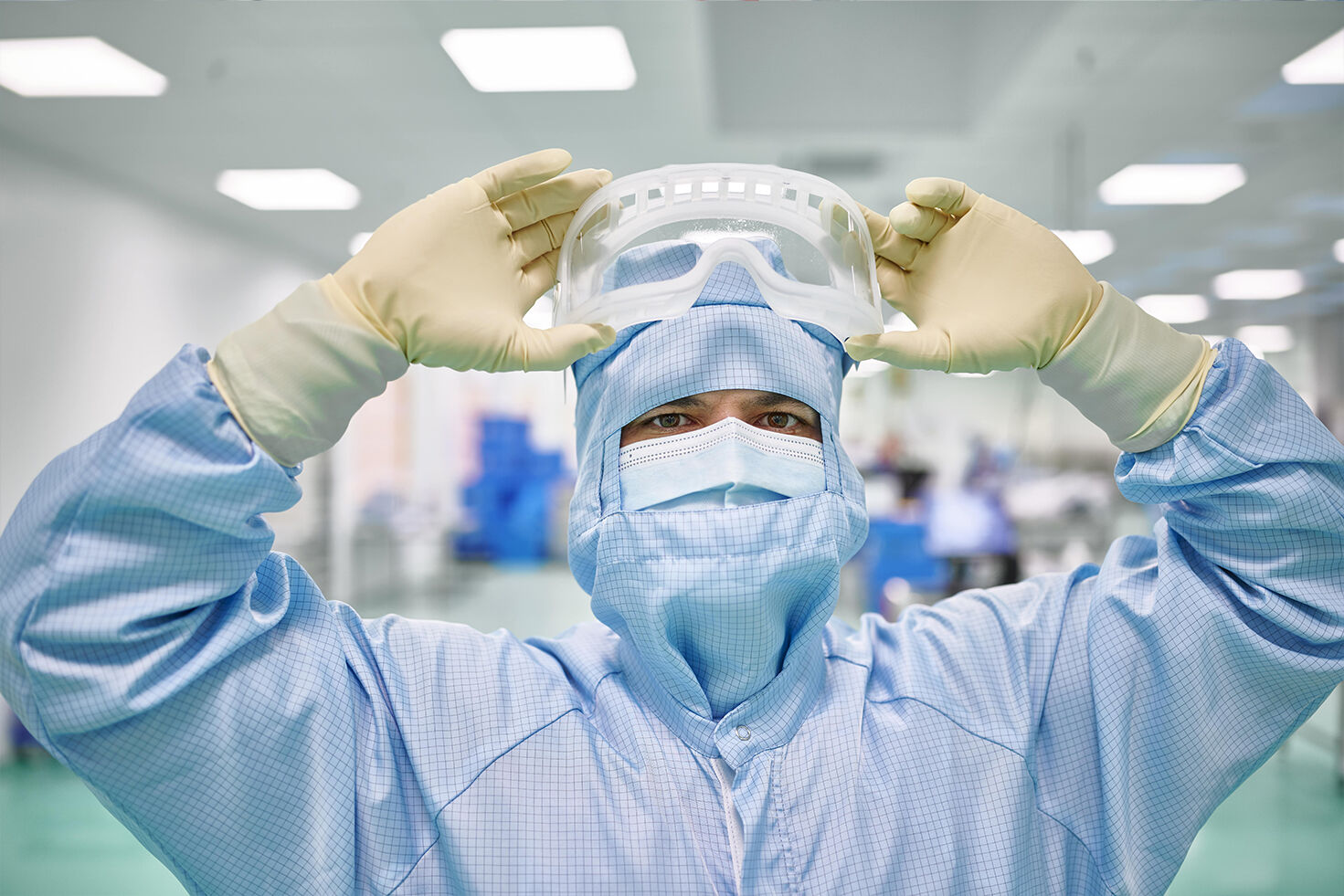